Refractory materials play a crucial role in the operation of furnaces across various industries. These materials are specially designed to withstand extreme temperatures, chemical attacks, and mechanical stresses, ensuring the efficient and safe functioning of furnaces.
One of the primary functions of refractory materials is to insulate the furnace interior from the outside environment. This helps in maintaining the high temperatures required for various processes such as metal melting, glass manufacturing, and chemical synthesis. Common types of refractory materials include fireclay, high alumina bricks, and magnesia-chrome bricks.
Fireclay refractories are widely used due to their relatively low cost and good thermal stability. They are suitable for applications where temperatures do not exceed 1600°C. High alumina bricks, on the other hand, offer superior resistance to high temperatures and are often employed in furnaces operating at temperatures above 1600°C. Magnesia-chrome bricks are known for their excellent resistance to basic slags and are commonly used in steelmaking furnaces.
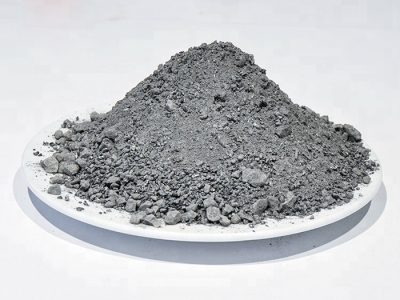
Refractory Materials
The selection of refractory materials depends on several factors such as the operating temperature of the furnace, the nature of the processed materials, and the chemical environment inside the furnace. It is essential to choose the right refractory to ensure long-term durability and performance.
In addition to providing thermal insulation, refractory materials also protect the furnace structure from damage caused by corrosive substances and mechanical abrasion. For instance, in the cement industry, where the raw materials are highly abrasive, refractories with high hardness and wear resistance are employed.
The quality and installation of refractory materials are of utmost importance. Poor-quality refractories or improper installation can lead to premature failure, resulting in costly downtime and production losses. Regular inspection and maintenance of the refractory lining are necessary to detect any signs of wear or damage and take corrective actions promptly.
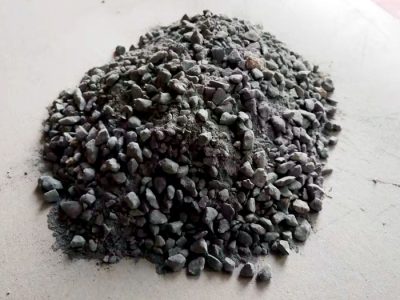
Refractory Materials
Advancements in technology have led to the development of new and improved refractory materials. Nanotechnology-based refractories, for example, offer enhanced properties such as better thermal shock resistance and lower porosity. These innovations are constantly driving the improvement of furnace performance and energy efficiency.
In conclusion, refractory materials are the backbone of furnace operations, enabling industries to carry out high-temperature processes efficiently and safely. The continuous research and development in this field will undoubtedly lead to more advanced and reliable refractory solutions in the future.