The characteristics of aluminum silicon carbide carbon bricks include high refractoriness, good thermal conductivity, high high temperature strength and excellent thermal shock resistance. Its uses include metallurgical industry, chemical industry, aluminum electrolytic cell lining and other fields.
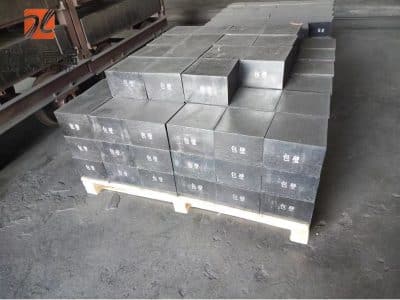
aluminum silicon carbide carbon bricks
Characteristics of aluminum silicon carbide carbon bricks:
High fire resistance:
Silicon carbide bricks themselves have extremely high refractoriness and can withstand the erosion of most chemicals, including acidic slag. Within the content range of 72% to 99%, its refractoriness increases as the SiC content increases.
When combined with silicon carbide bricks and high alumina silicon carbide bricks, the refractoriness is further improved. For example, the refractoriness of high-alumina silicon carbide bricks is greater than 1770°C, which allows it to withstand extremely high smelting temperatures without being damaged.
This kind of refractory material can maintain a high degree of stability and durability even without a binder, especially in replacing traditional refractory materials, showing significant advantages.
Good thermal conductivity:
Silicon carbide bricks have high thermal conductivity, which allows them to transfer heat quickly when used as kiln furniture or furnace linings, allowing for more efficient heating and cooling processes.
High-alumina silicon carbide bricks also exhibit excellent thermal conductivity, which is particularly important in furnace lining design in the metallurgical industry and can significantly improve energy efficiency and production efficiency.
High temperature strength:
Silicon carbide refractory materials can still maintain high strength at high temperatures, are not easy to soften, and can continue to withstand mechanical stress and chemical erosion at high temperatures.
In particular, silicon nitride-bonded silicon carbide bricks exhibit excellent mechanical properties in high-temperature applications, mainly due to their unique binding phase and dense microstructure.
Excellent thermal shock resistance:
Thermal shock resistance of a refractory material is its ability to withstand rapid temperature changes without damage. Silicon carbide bricks perform particularly well in this regard, mainly due to their low thermal expansion coefficient and excellent internal structural stability.
Recrystallized silicon carbide products can maintain structural integrity in rapid cooling and heating environments and are not prone to cracks, thereby extending service life and reducing maintenance costs.
https://www.lxrefractory.com/product/phosphate-bonded-brick
Strong resistance to slag corrosion:
The ability of refractory materials to resist slag corrosion determines their service life in chemically aggressive environments. Silicon carbide refractory materials have high stability to acidic slag and can effectively resist the erosion of chemical substances.
Due to its unique chemical composition and structure, high-alumina silicon carbide bricks exhibit good slag corrosion resistance, especially in certain industrial applications that require high slag resistance, such as lining materials for electrolyzers and smelting furnaces.
Uses of aluminum silicon carbide carbon bricks:
Metallurgical Industry:
Silicon carbide bricks are widely used as furnace lining materials in the metallurgical industry, such as steel drum linings, nozzles, plugs, etc. Its high refractoriness and slag corrosion resistance make these components more durable and effective.
Especially in the production of non-ferrous metallurgical retorts, aluminum casting molds, electric furnace linings, etc., silicon carbide bricks have become the preferred material due to their excellent performance.
Chemical Industry:
In the chemical industry, the acid, alkali and solvent resistance properties make silicon carbide refractory materials suitable for use as materials for distillers, distillation tower trays, electrolytic cell side walls and other parts.
The thermal conductivity and thermal shock resistance of silicon carbide bricks allow them to exhibit excellent performance and long service life when handling high-temperature chemicals.
Aluminum electrolytic cell lining:
In aluminum electrolytic cells, silicon carbide bricks are often used as the material selection for the cell lining due to their excellent corrosion resistance to liquid aluminum.
Silicon nitride combined with silicon carbide bricks are suitable for the cathode part of aluminum electrolytic cells due to their enhanced alkali resistance and oxidation resistance, helping to improve electrolysis efficiency and cell life.
Ceramic kiln furniture:
The unique properties of silicon carbide have led to its application in the ceramic manufacturing industry as kiln furniture materials, such as kiln shed boards, brackets and flame isolation materials.
The use of silicon carbide materials for kiln furniture not only increases the service life, but also improves the efficiency and quality of ceramic production, especially in situations where high-temperature sintering is required.
Energy and environmental protection fields:
High-alumina silicon carbide bricks and conventional silicon carbide bricks have shown their high efficiency and environmental protection value in the fields of energy and environmental protection, especially in facilities that require high-temperature treatment and heat-resistant protection, such as combustion furnaces and exhaust gas treatment equipment.
For practical application cases of aluminum silicon carbide carbon bricks, in-depth analysis can also be conducted from user feedback, material innovation research, and its potential development direction in future industrial applications. Considering the excellent performance of this material in extreme environments, there may be more breakthroughs in the fields of aerospace, high-performance building materials and other fields in the future.
In summary, aluminum silicon carbide carbon bricks have become the material of choice in many high-temperature application industries due to their unique physical and chemical properties. In the long run, with the advancement of technology and the development of materials science, its performance in existing application fields will be further optimized, and it may also be expanded to more high-tech fields.