The characteristics of carbon fired furnace bricks include high refractoriness, strong thermal stability, excellent physical properties, good energy-saving effect, and convenient construction. Its uses cover aluminum electrolytic cell lining materials, metallurgical industrial furnace linings, thermal equipment components, etc.
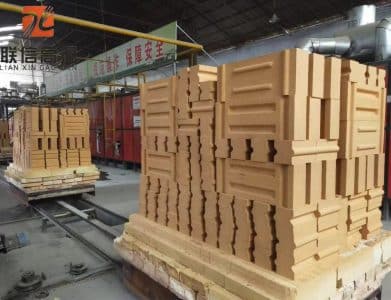
carbon fired furnace bricks
Features:
High refractoriness: Carbon fired furnace bricks have very high refractoriness and can withstand temperatures up to 1800°C, suitable for various high-temperature environments.
Strong thermal stability: This brick has excellent thermal stability and can withstand thermal shock in intermittent operation. After incomplete displacement recovery and brick misalignment, it can still maintain the integrity and functionality of the furnace wall.
Excellent physical properties: Carbon fired furnace bricks have high high-temperature flexural strength, and the cold strength after heating at 1300°C for half an hour is still excellent, showing excellent durability.
Good energy-saving effect: The furnace design using carbon fired furnace bricks helps to reduce heat loss, improve energy efficiency, and thus reduce production costs.
Convenient construction: The design of the new furnace interface measurement and control components and cross wall bricks makes construction and installation more mechanized and reduces labor intensity.
Application:
Lining material of aluminum electrolytic cell: Carbon roasting furnace bricks are one of the key components of aluminum electrolytic cells. They are used for masonry of furnace bottom, side walls and other parts to protect the furnace body and maintain the normal operation of the electrolytic cell.
Lining of metallurgical industrial furnaces: In the metallurgical industry, carbon roasting furnace bricks can be used as lining materials for a variety of industrial furnaces, such as ring roasting furnaces, etc., to provide necessary heat protection and thermal efficiency.
Thermal equipment components: Carbon roasting furnace bricks can also be used to construct other high-temperature thermal equipment, such as fire channel walls, furnace roofs and flues, because of their high requirements for refractoriness and thermal stability.
Improvement in energy consumption reduction: The structural design of carbon roasting furnace bricks helps to reduce heat loss. For example, the design of the furnace surface reducer cover can effectively reduce oil consumption, which has a significant impact on improving the economic and social benefits of enterprises.
Enhanced sealing and thermal insulation effect: The new design of special refractory castable structural parts enhances the sealing and thermal insulation effect of the cross wall, effectively reducing heat loss and scalding hazards.
In practical applications, the requirements for refractory materials for closed roasting furnaces and open roasting furnaces are slightly different, and it is necessary to select suitable refractory brick materials according to the specific structure and use conditions of the furnace type. For example, closed roasting furnaces generally use clay bricks with high mechanical strength and good thermal stability to build key parts, while open roasting furnaces often use lightweight refractory bricks to meet their specific use requirements.
In summary, carbon roasting furnace bricks play an important role in high-temperature industrial environments such as metallurgy and aluminum electrolytic cell lining materials due to their high refractoriness, strong thermal stability, excellent physical properties, good energy-saving effect, and convenient construction. By continuously optimizing the furnace design and material selection, the thermal efficiency can be further improved, energy consumption can be reduced, and greater economic and environmental benefits can be brought to enterprises.