The metallurgical industry relies heavily on the use of refractory bricks in the construction and maintenance of metal smelting furnaces. These specialized bricks are the backbone of the furnaces, providing the necessary protection and performance to carry out the smelting process effectively. This article delves into the reasons behind the critical role of refractory bricks in metal smelting operations
The Need for Extreme Heat Resistance
Metal smelting is a high-temperature process where metal ores are heated to melting points ranging from 1000°C to over 1600°C. The primary reason for using refractory bricks is their ability to withstand these extreme temperatures without losing their structural integrity. The high refractoriness of these bricks, often exceeding 1700°C, makes them ideal for the intense heat generated in smelting furnaces.
Chemical Inertia and Purity
Refractory bricks are chemically inert, meaning they do not react with the molten metal or the slag produced during the smelting process. This inertness is crucial for maintaining the purity of the metal, as any reaction with the furnace lining could lead to contamination of the final product.
Thermal Shock Resistance
Smelting furnaces are subject to frequent temperature fluctuations, from the initial heating to the cooling down phases. Refractory bricks must be able to endure these rapid changes without cracking or breaking. The thermal shock resistance of these bricks ensures the furnace lining remains intact, even under the stress of sudden cooling.
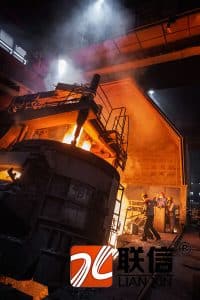
Metal Smelting Furnaces
Structural Stability and Load Bearing
The furnace lining must support the weight of the furnace structure and the molten metal. Refractory bricks provide the necessary mechanical strength and rigidity to bear these loads without deformation. This stability is essential for the safe operation of the furnace.
Durability and Longevity
The longevity of a furnace lining directly impacts the operational costs and downtime of a smelting operation. Refractory bricks are designed for long-term use, resisting wear, erosion, and corrosion from the molten metal and slag. This durability reduces the frequency of repairs and replacements, leading to cost savings and increased efficiency.
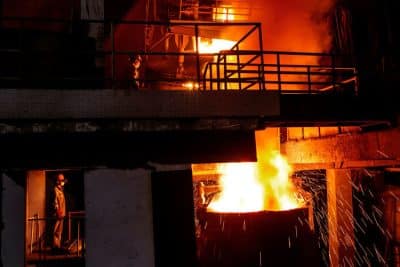
Metal Smelting Furnaces
Energy Efficiency
In addition to their protective qualities, refractory bricks contribute to the energy efficiency of the furnace. By providing excellent insulation, they minimize heat loss, ensuring that the majority of the energy input is used for the smelting process rather than being wasted through the furnace walls.
Safety Considerations
The use of refractory bricks in metal smelting furnaces is not only about performance but also about safety. These bricks act as a barrier between the workers and the extreme conditions inside the furnace, reducing the risk of accidents and ensuring a safer working environment.
Conclusion
Refractory bricks are a fundamental component in the design and operation of metal smelting furnaces. Their unique properties of high-temperature resistance, chemical inertness, thermal shock resistance, structural stability, durability, and energy efficiency make them indispensable in the metallurgical industry. As technology advances, the development of more advanced refractory materials continues to push the boundaries of what is possible in metal smelting, ensuring the industry remains efficient, safe, and sustainable.